Что такое лазерная резка
В этой статье вы узнаете о процессе лазерной резки и о том, где она находит применение в производстве.
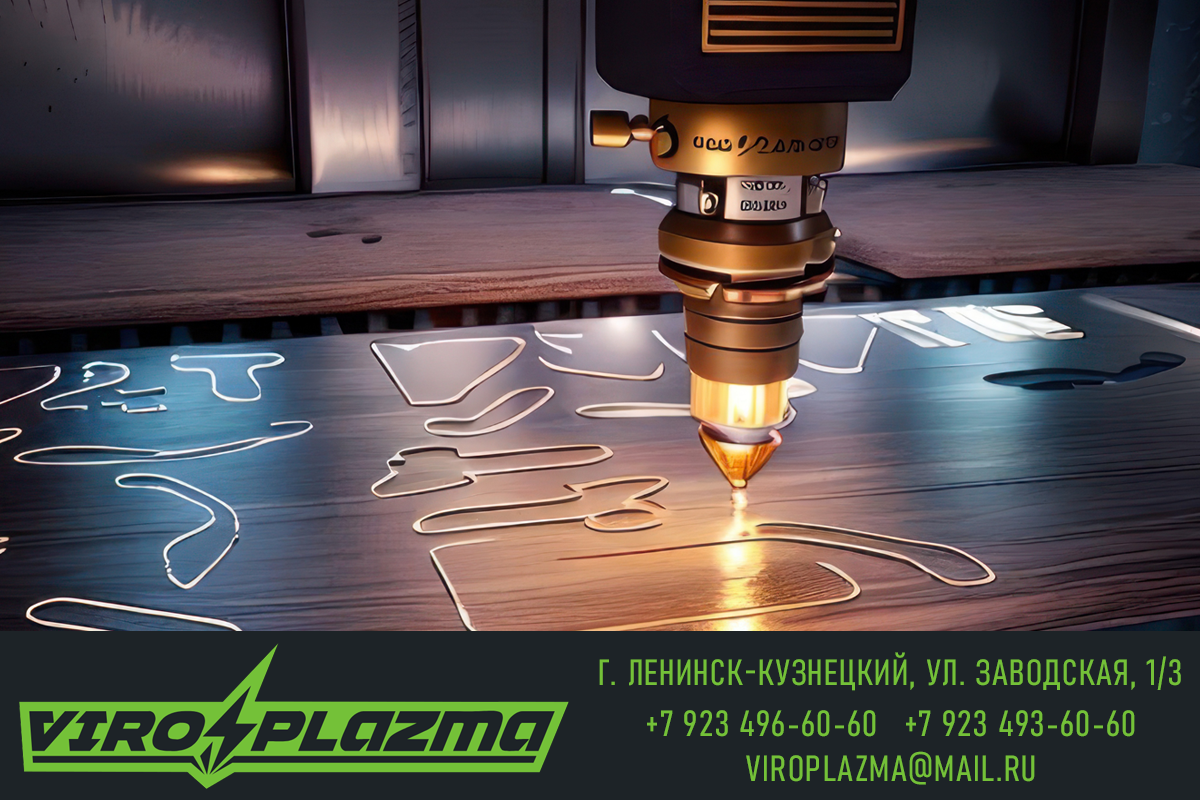
Лазерный станок это устройство, в котором применяется высокоэнергетический сфокусированный лазерный луч для резки различных листовых или пластинчатых материалов. С его помощью можно создавать двухмерные детали как для хобби, так и для промышленных целей. Типичные материалы, которые поддаются лазерной резке, включают в себя дерево, сталь и некоторые виды пластмасс.
Лазер – это аббревиатура, которая расшифровывается как «Усиление света через стимулированное излучение». Это термин, описывающий физическую основу генерации лазерного света.
Хотя фундаментальная физика лазеров остается неизменной, существует три основных типа реализации этой технологии: СО2 – лазеры, волоконные лазеры и Nd:YAG – лазеры.
В этой статье «Лазерная резка» мы подробно рассмотрим процесс лазерной резки. Мы расскажем, как лазерный луч генерируется и направляется на материал, который необходимо разрезать. Кроме того, мы объясним, в чем заключается различия между различными технологиями лазерной резки.
Процесс лазерной резки на станке
Станок для лазерной резки функционирует, фокусируя очень тонкий и мощный световой луч по вертикали вниз на листе или пластине материала. Этот луч разрезает материал в виде двухмерного профиля, перемещаясь в направлениях X и Y вдоль направляющей внутри станка.
Луч расплавляет или прожигает материал в соответствии с заранее определенным шаблоном, который задается набором компьютерных инструкций, известных как G-код. Иногда для выдувания расплавленного материала из нижней части разрезаемой детали применяется поток газа под высоким давлением. Этот процесс позволяет избежать накопления отходов в области разреза и их затвердевания после перемещения луча. В некоторых случаях лазерный луч просто испаряет материал. Метод генерации лазерного луча может различаться в зависимости от технологии, но в целом все они включают следующие основные этапы:
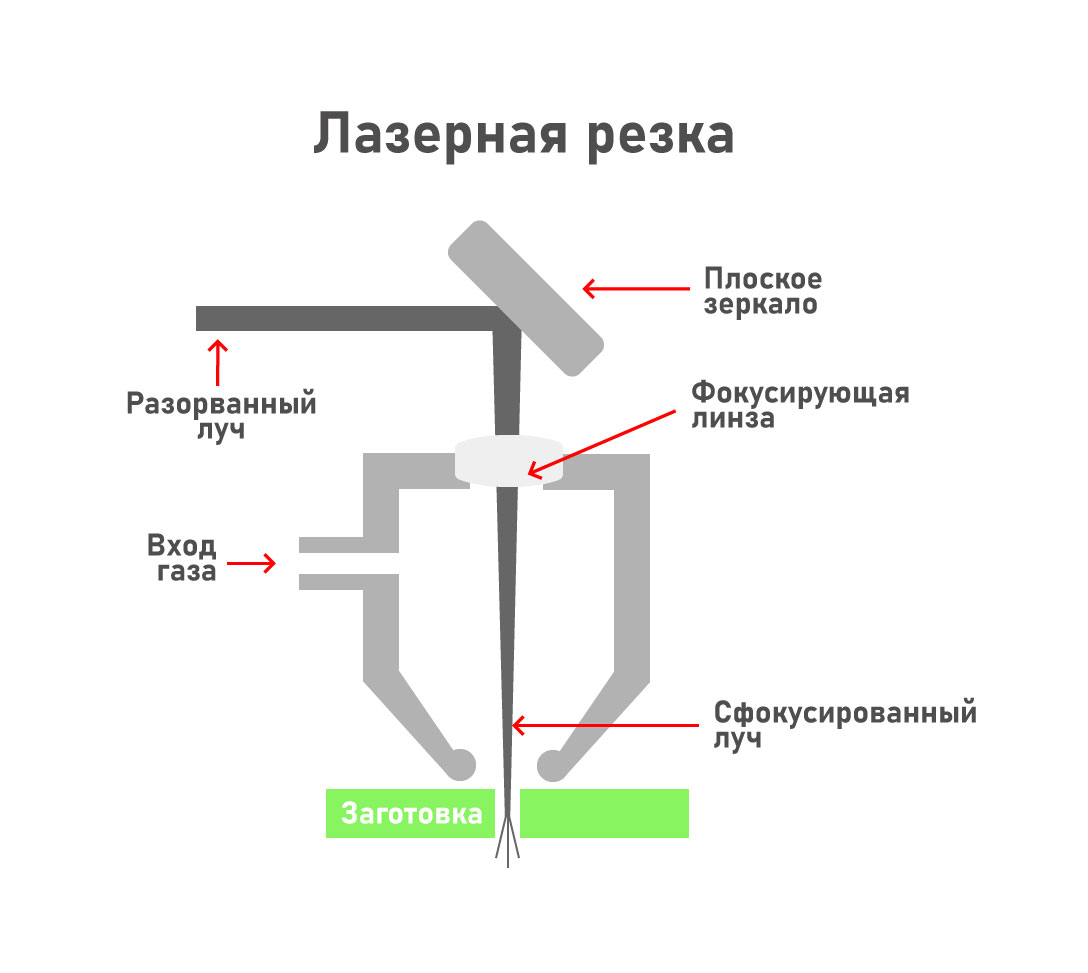
Этап 1: Создание G-кодового файла для станка лазерной резки
Перед тем как приступить к процессу лазерной резки на станке, необходимо разработать G-код для управления работой оборудования станка лазерной резки. G-код — это набор специальных инструкций, понятных машине, которые определяют движения головки станка лазерной резки.
Для простых форм оператор может создавать инструкции вручную. Однако для более сложных конструкций требуется использование программного обеспечения CAM (Computer-Aided Manufacturing), которое автоматически генерирует G-код на основе файла CAD (Computer-Aided Design). Этот G-код затем отправляется на машину через Wi-Fi-соединение или USB-накопитель.
Этап 2: Формирование лазерных лучей
Лазерный луч создается внутри резонатора. Различные лазерные технологии используют разные среды для генерации лазерного излучения, но физика процесса остается неизменной для всех типов лазеров.
Когда электрон сталкивается с фотоном, он поглощает его энергию, чтобы перейти в более высокое энергетическое состояние. Точное количество энергии от фотона необходимо для того, чтобы зарядить электрон в определённом энергетическом состоянии. Этот процесс известен как стимулированное поглощение.
Однако, через очень короткий промежуток времени электрон начинает распадаться на более низкую орбитальную. Этот распад происходит из-за небольших флуктуаций в квантовом вакууме, которые возвращают его в более низкое энергетическое состояние. В процессе распада электрон испускает фотон, что является свидетельством его возвращения. Этот процесс называется спонтанной эмиссией.
Процесс спонтанного излучения фотона не подходит для создания лазерного луча, так как испускаемые фотоны будут двигаться в разных направлениях и не будут иметь последовательного направления. Кроме того, они быстро вернутся в исходное состояние.
Лазеры решают эту проблему, используя материалы с метастабильным состоянием. Это позволяет электронам оставаться в полувозбуждённом состоянии дольше, чем при спонтанном излучении — в течение миллисекунд вместо наносекунд.
Когда фотон вступает во взаимодействие с электроном, который уже находится в возбуждённом метастабильном состоянии, это может привести к тому, что электрон вернётся на более низкую энергетическую орбиту. В процессе такого возвращения выделяется фотон с теми же характеристиками, что и у фотона, который изначально его возбудил: той же частотой, фазой и поляризацией. Этот процесс известен как стимулированное излучение и является основой для создания лазерного луча.
Как только начинается стимулированное излучение, высвобождается целый каскад фотонов, которые затем распространяются по трубке.
Этап 3: Лазерное усиление.
Когда начинается процесс спонтанного излучения, фотоны движутся в случайном направлении. Однако некоторые из них попадают перпендикулярно двум зеркалам, расположенным на обоих концах лазерной среды. В результате возникают две световые волны — одна движется влево, а другая — прямо в среде. Эти волны образуют стоячую волну, которая представляет собой комбинацию конструктивных и разрушительных колебаний.
Когда стоячие волны достигают резонанса, интенсивность света значительно возрастает. Полуотражающее зеркало начинает пропускать через себя часть света, создавая когерентный луч лазерной энергии. Оставшийся свет продолжает отражаться в лазерной среде, обеспечивая непрерывное стимулированное излучение фотонов.
Различные лазерные технологии позволяют создавать лазеры с различными длинами волн.
Этап 4: Направление и фокусировка луча
После усиления в лазерной среде луч выходит наружу. В зависимости от типа лазера, он либо проходит через волоконно-оптический кабель (как в случае волоконного лазера), либо через серию зеркал (как в случае лазеров CO2 и Nd:YAG).
Далее луч попадает на листовой материал через линзу, которая фокусирует его энергию в очень маленькую точку, создавая локальный источник высокой энергии. Важно отметить, что лазер имеет только одну точку фокусировки с высокой интенсивностью; весь луч не обладает одинаковой мощностью для резки. Из-за этой разницы в интенсивности лазерные резаки имеют ограничения по толщине материала, который они могут разрезать, так как интенсивность лазера снижается выше и ниже точки фокусировки.
Этап 5: Резка материала.
Как только луч лазера сфокусируется, он начинает плавить или испарять материал. Если речь идёт о неплавящихся материалах, таких как древесина, лазер просто прожигает в них отверстие.
В случае с металлами лазерный луч сначала расплавляет их, а затем струя газа под высоким давлением выдувает расплавленный материал из зоны разреза. Этот газ может быть инертным азотом, аргоном или кислородом, который используется для ускорения процесса резки стали.
Методы и технологии лазерной резки
В целом, лазерный резак предназначен для фокусировки энергии в небольшом участке материала, чтобы испарить или расплавить его. Однако способ, которым эта энергия доставляется, может различаться. Ниже представлены некоторые из наиболее распространенных видов лазерной резки:
Резка плавлением
В процессе резки плавлением используется струя инертного газа высокого давления, например, аргона или азота, для удаления расплавленного материала из разреза, созданного лазерным лучом. Инертный газ выбирается для того, чтобы не вступать в реакцию с расплавленным металлом. Он также служит защитным газом для расплавленной кромки.
Газовая резка
Не следует путать с кислородно-ацетиленовой резкой, лазерная резка с использованием пламени отличается тем, что в ней кислород выступает в качестве вспомогательного элемента. Он способствует процессу резки, вызывая экзотермическую реакцию окисления, что позволяет снизить энергозатраты лазера. Кислород также используется для физического удаления расплавленного материала из области реза. Этот процесс также известен как реактивная лазерная резка.
Дистанционная резка
Дистанционная резка, также известная как сублимационная или испарительная, применяется для обработки очень тонких или деликатных материалов. В этом процессе газ не применяется, а лазер обычно перемещается с помощью гальванического сканера, который направляет луч через серию зеркал. Вместо того чтобы газ выдувал расплавленный материал, лазер испаряет или аблирует его. Дистанционная резка может быть очень быстрой, особенно на тонких материалах.
Разрушение под воздействием термического напряжения
Резка с термическим стрессовым разрушением — это технология, которая позволяет разрезать материал, создавая напряжение в его основе. Одним из примеров может служить метод, применяемый для резки нитрида алюминия. В этом процессе несфокусированный луч расплавляет очень тонкий слой материала на поверхности детали, образуя оксид алюминия.
Оксид алюминия и базовый нитрид алюминия обладают разными коэффициентами теплового расширения. Когда эти материалы остывают с различной скоростью, возникает напряжённое поле, которое приводит к растрескиванию детали вдоль лазерной линии.
Векторная резка
Векторная резка — это метод лазерной резки, применяемый для создания деталей, состоящих из чистых линий. Хорошим примером такой резки могут служить рекламные вывески. В этом процессе лазер проникает через материал насквозь.
Лазерная растрировка — это наиболее распространённый способ гравировки изображений на поверхности материалов. Она работает следующим образом: на входе подаётся растровое изображение, которое затем преобразуется в набор инструкций для лазерного резака. Следуя этим инструкциям, лазер выжигает изображение на базовом материале.
Типы лазеров, применяемых в лазерной резке
В процессе лазерной резки обычно используются три основных типа лазеров. CO2-лазеры функционируют на основе углекислого газа (CO2), который смешивается с другими инертными газами, выступая в качестве активной среды. В свою очередь, твердотельные волоконные и Nd:YAG-лазеры используют кристалл в качестве лазерной среды. Несмотря на различия в материалах, принцип работы этих лазеров остается в целом схожим.
Лазеры CO2
Лазер на углекислом газе (CO2) состоит из трубки, в которой заключены CO2, гелий и азот. Добавление азота и гелия позволяет повысить эффективность лазера. Азот служит временным хранилищем энергии, которая впоследствии может быть передана молекуле CO2, как только она испускает фотон. Гелий, с другой стороны, отбирает всю оставшуюся энергию у молекулы CO2, передавая ей кинетическую энергию после того, как она излучает фотон. Это позволяет ей вновь получать энергию от молекулы азота.
На одном конце трубки расположено полностью отражающее зеркало, а на другом — частично отражающее. Газ в трубке ионизируется под воздействием сильного электрического поля, что приводит к генерации света. Сильное электрическое поле заставляет электроны в молекулах CO2 переходить в более высокое энергетическое состояние, создавая фотоны.
Когда фотон приближается к атому в возбужденном состоянии, он заставляет этот атом испускать еще один фотон. Эти фотоны затем отражаются от двух зеркал, пока не накопится достаточное количество для прохождения через полуотражающее зеркало.
Для оптимальной эффективности температура в трубке должна поддерживаться на низком уровне. Поэтому трубка охлаждается с помощью низкотемпературного газа или жидкости. В некоторых системах газ перерабатывается, что позволяет снизить эксплуатационные расходы.
CO2-лазеры работают на длине волны 10600 нм и являются превосходными лазерами общего назначения, способными резать множество материалов, включая листовой и пластинчатый металл. Однако они могут испытывать трудности с материалами с высоким теплопоглощением и с высокой отражательной способностью.
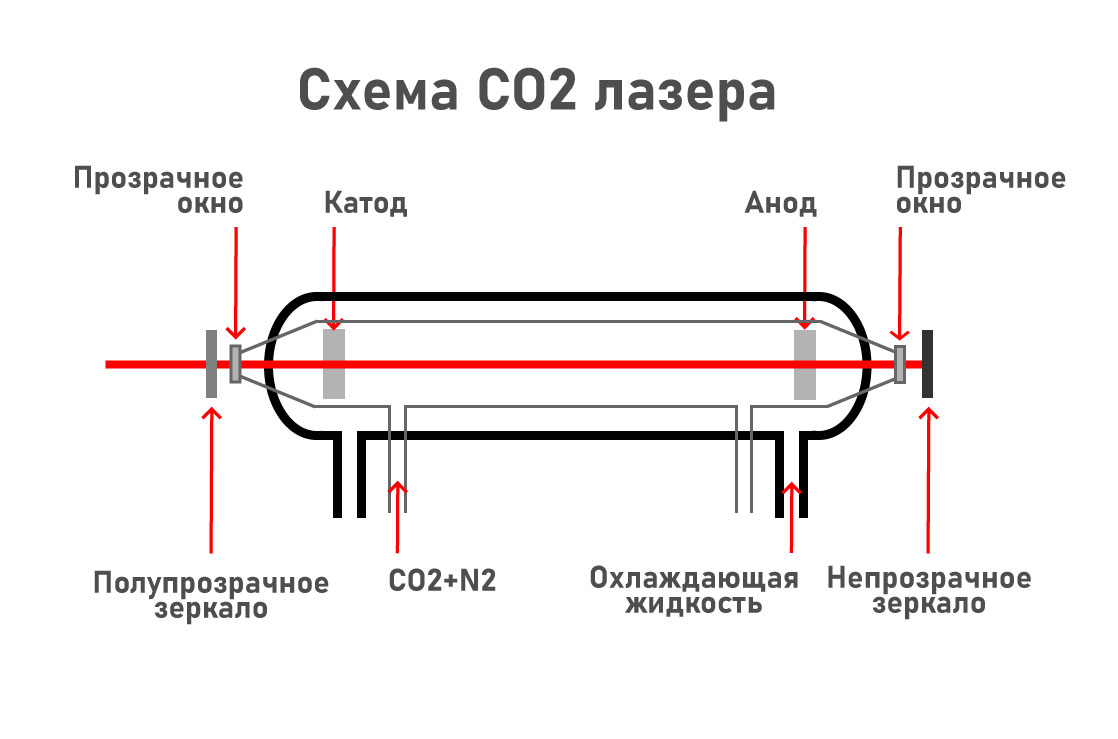
Волоконные лазеры
Волоконные лазеры работают с использованием волоконно-оптического кабеля, который был специально обработан и дозирован. Луч волоконного лазера возникает в результате накачки фотонов в один конец этого кабеля, который обычно состоит из кварцевого или боросиликатного стекла.
Фотоны движутся по волокну, пока не достигают области, которая была обработана редкоземельным элементом. Наиболее часто используемые элементы включают неодим, иттрий, эрбий или тулий. Каждый из этих элементов создает лазер с уникальной длиной волны при возбуждении фотонами.
Затем свет усиливается с помощью волоконных брэгговских решеток, которые выполняют ту же функцию, что и отражающие и полуотражающие зеркала в лазерах Nd:YAG и CO2. Эти решетки отражают свет вперед и назад, что приводит к образованию каскада фотонов. Как только интенсивность достигает определенного уровня, свет может свободно проходить через решетку, формируя высокоинтенсивный когерентный луч света.. Как и другие лазеры, волоконный лазер использует газ для удаления расплавленного материала с пути лазерного луча или для улучшения процесса резки.
Волоконные лазеры, как правило, имеют более короткую длину волны, что обеспечивает более высокое поглощение. Это делает их идеальными для резки отражающих материалов и способствует меньшему выделению тепла в процессе. Именно поэтому волоконные лазеры идеально подходят для обработки отражающих материалов, а также для материалов, хорошо поглощающих тепло, таких как медь или золото.
Гибкость волоконно-оптического кабеля позволяет легко устанавливать волоконную режущую головку на шестиосевые роботизированные манипуляторы, не требуя использования нескольких зеркал для направления лазерного луча, как это необходимо для лазеров CO2 или Nd:YAG. Волоконные лазеры отличаются более высокой электрической эффективностью по сравнению с лазерами CO2.
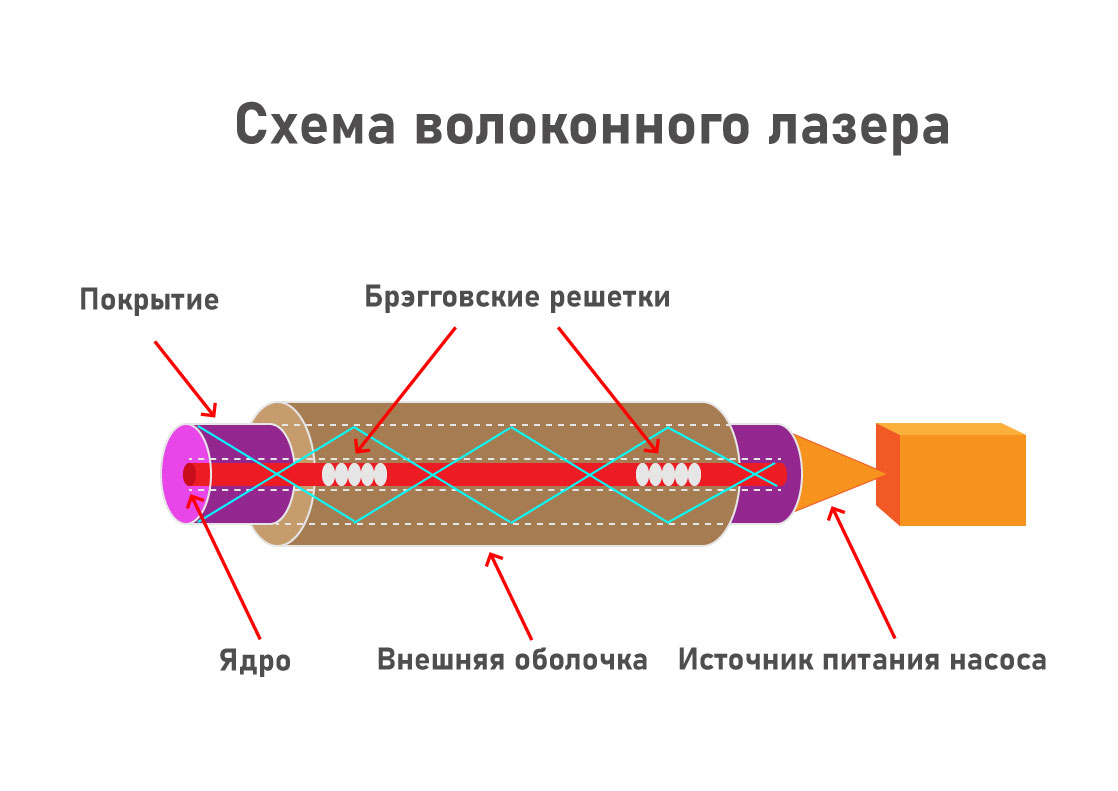
Лазеры Nd:YAG/Nd:YVO
Лазер Nd:YAG представляет собой устройство, в основе которого лежит кристалл иттрий-алюминиевого граната, легированный неодимом (Nd). Этот кристалл имеет формулу Y3Al5O12. В процессе легирования часть ионов иттрия (примерно 1%) замещается ионами Nd3+.
Кристалл располагается между двумя зеркалами — одним полностью отражающим и другим полуотражающим. Источником фотонов накачки может служить ксеноновая/криптоновая импульсная лампа или ряд лазерных диодов.
Когда источник накачки посылает фотоны в кристалл Nd:YAG, они повышают уровень энергии ионов неодима. В результате ионы распадаются, испуская каскад фотонов, которые, отражаясь между зеркалами, формируют когерентный лазерный луч.
Этот луч характеризуется высокой интенсивностью и частотой 1064 нм. С помощью зеркал он направляется на режущую головку и, наконец, фокусируется в точку с помощью линзы на режущей головке.
Лазеры Nd:YVO, использующие кристаллы ванадата, легированные неодимом (YVO4), функционируют аналогичным образом, как и лазеры Nd:YAG.. Тем не менее, лазеры Nd:YVO отличаются повышенной стабильностью мощности, не производят много тепла и способны генерировать больше импульсов в секунду.
Лазеры Nd:YAG, в сравнении с волоконными лазерами, обладают лучшим качеством луча и более высокой плотностью мощности, что делает их идеальными для маркировки и травления. Однако у лазеров Nd:YAG есть существенный недостаток — более высокие эксплуатационные расходы и не всегда высокая энергетическая эффективность.
Распространенное применения лазерной резки
Лазерные резаки представляют собой универсальное производственное оборудование, применяемое в различных областях, как описано ниже:
1. Резка листового металла: Лазерные резаки широко используются для обработки как листов, так и пластин из различных материалов, включая металлы, пластик и дерево.
2. Гравировка: Лазеры могут быть использованы для маркировки практически любого материала. Их применяют как для добавления серийных номеров к готовым деталям, так и для более художественных целей, например, для маркировки дерева.
3. Лазерная сварка: Этот метод позволяет точно соединить два металла или термопласта, используя лазерный луч вместо электрической дуги.
4. Резка труб: Лазерные станки с вращающейся осью предназначены для обработки сложных профилей на полых секциях.
Преимущества лазерной резки
Лазерная резка — это широко используемая производственная технология, которая имеет множество преимуществ. Ниже мы рассмотрим некоторые из ключевых достоинств, которые делают лазерные резаки столь востребованными в промышленности:
Универсальность материалов: Лазерные резаки способны обрабатывать практически любой материал. Толщина материала, который можно разрезать с помощью лазера, зависит от мощности лазера, лазерной технологии и характеристик самого материала.
Ограниченная постобработка: Детали, полученные с помощью лазерной резки, не требуют значительных дополнительных манипуляций. Однако в некоторых случаях, например, при резке металла, может потребоваться зачистка кромок реза, так как на них может образоваться шлак.
Узкие разрезы: Лазеры могут фокусироваться на очень тонких лучах, что позволяет получать чрезвычайно узкие разрезы. Ширина реза может составлять всего 0,1 мм, что зависит от материала и его толщины.
Преимущества лазерных станков
Высокая точность
Лазерные станки не испытывают никаких нагрузок на режущую головку, в отличие от других технологий, таких как фрезерные станки с ЧПУ. Это делает их невероятно точными и аккуратными в своей работе.
Высокая скорость
Лазерные станки способны очень быстро создавать 2D-профили. Они могут резать мягкие материалы, такие как пластик, на высоких скоростях, что значительно ускоряет процесс производства.
Автоматизация
Лазерные станки отличаются высокой степенью автоматизации. Некоторые модели могут самостоятельно загружать сырье на режущий стол и выгружать готовые детали, минимизируя участие человека в процессе.
Стоимость инструментов
В отличие от обработки с ЧПУ, лазерные станки не требуют большого количества инструментов. Износ инструментов из-за трения отсутствует, поскольку головка лазерного станка не контактирует с сырьем, что значительно снижает затраты на инструменты.
Отсутствие зажимов
Лазерным станкам не нужны зажимы или другое зажимное оборудование для резки. Материал можно просто положить на режущий стол, и он останется неподвижным во время процесса.
Недостатки лазерной резки
Несмотря на множество преимуществ, лазерная резка также имеет некоторые ограничения, которые следует учитывать:
Высокое энергопотребление: Этот процесс требует значительного количества энергии, особенно если речь идет о таких технологиях, как резка лазером CO2.
Ограниченная толщина: Из-за особенностей фокусировки лазерного луча в точке высокой интенсивности, лазерные резаки имеют ограничения по толщине разрезаемых материалов. Как правило, они могут обрабатывать только листовые и пластинчатые материалы с максимальной толщиной до 25 мм. Хотя возможно резать и более толстые материалы, это обычно не практикуется в стандартных производственных цехах.
Опасные пары: При резке некоторых материалов, таких как дерево или пластик, могут образовываться опасные дымовые газы, которые требуют специальных мер по удалению.
Дорогостоящее обслуживание: Некоторые лазерные технологии, такие как CO2, рассматривают лазерную трубку как изнашиваемый элемент, который необходимо регулярно заменять, что влечет за собой значительные расходы.
Высокая первоначальная стоимость: инвестирование в лазерные резаки требует значительных финансовых вложений. В некоторых ситуациях более доступные альтернативы, такие как газовые или плазменные резаки, могут оказаться более эффективными.
Распространенные материалы для лазерной резки
Лазерные резаки открывают двери к обработке самых разных материалов. Ниже представлены некоторые из наиболее популярных материалов, которые чаще всего подвергаются лазерной резке:
Акрил (ПММА)
Акрил отличается гладкой режущей кромкой, однако для его обработки необходима специальная вытяжная система, так как в процессе резки выделяются легковоспламеняющиеся пары. Давление газа должно быть отрегулировано таким образом, чтобы оно эффективно удаляло пары и одновременно охлаждало режущую кромку для ее затвердевания. Избыточное давление воздуха может деформировать режущую кромку, пока она еще находится в расплавленном состоянии.
Углеродистая сталь/мягкая сталь
Углеродистая сталь представляет собой широкий спектр сталей, основным легирующим элементом которых является углерод. Мягкая сталь — это особый тип углеродистой стали с содержанием углерода менее 0,3%. Чем выше содержание углерода, тем прочнее сталь. Мощные лазеры способны разрезать пластины толщиной до 20–25 мм.
Нержавеющая сталь
Нержавеющая сталь — это особый вид стального сплава, который содержит хром и/или никель в качестве основных легирующих элементов. Благодаря своей устойчивости к широкому спектру химических веществ, нержавеющая сталь широко применяется в различных отраслях. Её легко разрезать с помощью любой технологии лазерной резки, но лучше всего использовать волоконный лазер.
Алюминий
Алюминий представляет собой общий термин, который охватывает множество алюминиевых сплавов с различными добавками и областями применения. Этот материал отличается хорошим соотношением прочности и веса, что делает его популярным в аэрокосмической промышленности. Однако в расплавленном состоянии алюминий обладает отражающими свойствами, что затрудняет его резку. Тем не менее, алюминий можно разрезать с помощью CO2-лазера, но для достижения наилучших результатов рекомендуется использовать волоконный лазер.
Латунь
Латунь — это сплав меди с цинком и другими элементами. Она обладает высокой прочностью и долговечностью, что делает её незаменимым материалом в различных отраслях. Латунь легко режется с помощью технологии лазерной резки, позволяя создавать точные и сложные формы.
Латунь представляет собой сплав меди и цинка с добавлением нескольких дополнительных легирующих элементов. Этот материал отличается высокой устойчивостью к коррозии, электропроводностью и низким коэффициентом трения, что делает его идеальным для применения в различных сферах, включая втулки с низким коэффициентом трения и электротехнические изделия.
Дерево
Дерево легко поддается лазерной резке, особенно с использованием CO2-лазеров средней мощности (150–800 Вт). Однако для обеспечения безопасности необходимо установить вытяжную систему, так как в процессе лазерной резки дерева образуется дым. Натуральная древесина имеет зернистую структуру, что может привести к неравномерной отделке при гравировке или резке. Тем не менее, лазеры могут обрабатывать как твердые, так и мягкие породы дерева.
ДВП
ДВП, или древесноволокнистая плита высокой плотности, напоминает МДФ (древесноволокнистую плиту средней плотности), но обладает большей плотностью, что делает его более прочным и надежным выбором. Волокна древесины в ДВП скреплены клеем, который испаряется во время резки, что требует использования вытяжной системы для обеспечения безопасности. ДВП характеризуется однородностью, что позволяет выполнять резку и гравировку последовательно.
Пробка
Пробка — это мягкий древесный материал, получаемый из коры пробкового дуба. Она широко используется для создания вставок в обувь, нескользящих подставок и досок для заметок. Пробку очень легко резать лазером и гравировать.
Кожа
Кожа — это прочный и износостойкий натуральный материал, который применяется в производстве обуви, ремней и кошельков. Её легко обрабатывать лазером и гравировать, что делает возможным создание уникальных персонализированных изделий. Стоит отметить, что существуют синтетические аналоги кожи, известные как искусственная кожа. Однако стоит учитывать, что некоторые из них могут содержать ПВХ, который при лазерной резке выделяет вредные пары.
Войлок
Войлок — это плотный и мягкий материал, который получают из шерсти животных. Он широко используется для изготовления ковриков, утеплителей и подкладок. Войлок легко поддается лазерной резке и гравировке, что делает его привлекательным для дизайнеров и производителей.
Войлок представляет собой недорогой нетканый материал, который довольно сложно разрезать вручную, но зато его можно легко обработать лазерным резаком. Этот материал широко применяется для изготовления одежды, декоративных нашивок и ковриков под столовые приборы.
Рекомендуется использовать войлок, состоящий на 95-100% из шерсти, так как синтетический войлок, часто содержащий акрил, плохо поддаётся резке.
Материалы, которые нельзя резать на лазерном станке
Не все материалы подходят для лазерной резки, а некоторые из них могут даже выделять вредные газы в процессе обработки. В этой статье мы рассмотрим некоторые материалы, которые не следует использовать для лазерной резки:
1. Ламинированное стекловолокно — Стекловолокно и эпоксидная смола часто образуют плохо режущийся материал, поэтому данный материал не рекомендуется для лазерной резки.
2. Полиэтилен высокой плотности — Этот материал будет плавиться, а не испаряться, что делает его неподходящим для лазерной резки.
3. Полистирол и полипропиленовая пена — Эти пены могут воспламеняться при лазерной резке, что представляет опасность для оператора и окружающих.
4. Акрилонитрилбутадиенстирол (ABS) — Этот материал также будет плавиться, а не испаряться, и может выделять токсичный цианистый газ во время резки.
5. Поливинилхлорид — При лазерной резке поливинилхлорид выделяет хлорный газ, что может привести к коррозионным повреждениям оптики и оборудования для лазерной резки.
6. Поликарбонат — листы поликарбоната толщиной более 1 мм могут воспламеняться при резке, а также обесцвечиваться.
Опасности лазерной резки
Как и большинство промышленных машин, лазерные резаки могут представлять определенные риски, о которых следует помнить:
1. Возгорание: Если лазерная резка некоторых материалов, таких как дерево, осуществляется неправильно, это может привести к возгоранию.
2. Токсичные газы: При резке некоторых материалов выделяются токсичные или едкие пары, что требует особого внимания и соблюдения мер предосторожности.
3. Повреждение глаз: При работе с материалами с высокой отражающей способностью существует риск того, что лазерный луч может отразиться и попасть в глаза, что может вызвать серьезные повреждения.
4. Острые режущие кромки: Лазерный резак может создавать острые режущие кромки, которые, если их не зачистить или не обращаться с ними должным образом, могут стать причиной серьезных порезов.